High Pressure Slip Casting System
High pressure slip casting (HPSC or HPC)
HPC is a high-performance mass production system used to produce ceramic parts cost-efficiently with high density, strength, and dimensional accuracy. HPC systems are designed in case to produce sanitary ware, tableware and technical ceramics using high-pressure injection of clay slip (porcelain, stoneware, bone china, vitreous china (VC), fine fire clay (FFC)) into porous resin molds.
Porous resin molds are used in high-pressure casting because they allow for the easy release of the clay body after it has been cast. The porous surface of the resin mold allows air and water to escape during the casting process, preventing air pockets or other defects from forming in the final product. However, there are some limitations to using porous resin molds in high pressure casting. First, the porous surface can absorb some of the ceramic slurry, which can lead to variations in the density and strength of the final part. Second, the pores in the resin mold can become clogged over time, reducing the quality of the cast parts.
To overcome these limitations, it is important to choose a high-quality resin material as offered by Castimo that is resistant to absorption and clogging. It is also important to properly maintain and clean the molds to ensure consistent casting results.
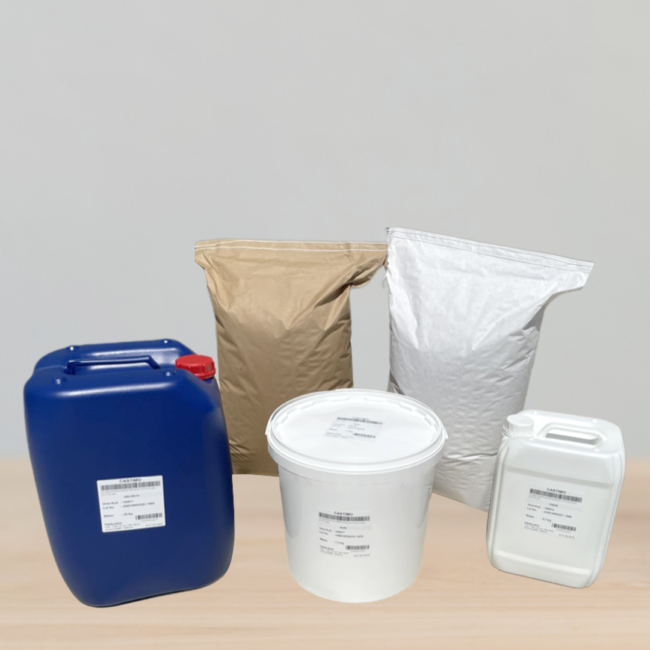
Steps of High Pressure Slip Casting (Sanitary Ware)
The steps involved in high pressure slip casting are usually as follows:
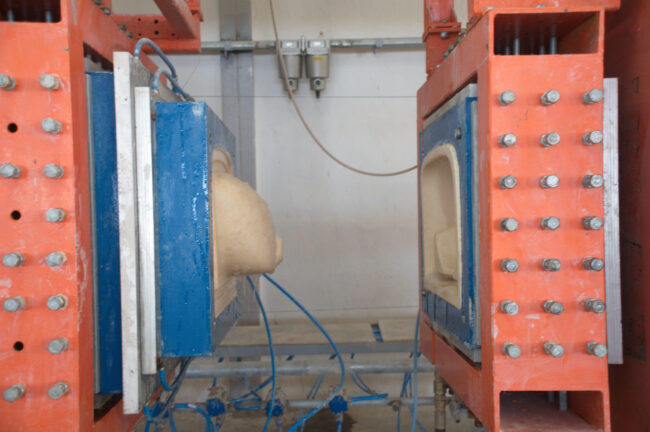
- Mold preparation: The resin molds installed in the machinery must be clean and coated with a release agent to prevent the slip from sticking to the mold surface. An HPC machine uses water and air pressure to ensure that porous resin molds are cleaned between each cycle.
- Injection of the slip: The HPC machine will close the 2- or more part resin mold and the filling with slip starts. After pre-filling with slip pressure of 3 to 4 bars, the final slip pressure raises between 10 to 13 bars. The high pressure helps to overcome the resistance of the slip to flow into complex mold shapes and narrow features.
- Solidification: As the slip fills the mold, excess water is forced out through small pores in the porous resin mold surface, leaving behind a solid ceramic part with minimal shrinkage. The clay body formation process will be stopped when the required clay thickness is reached.
- Demolding: Once the clay body has solidified, the mold is opened and the clay body is carefully removed from the Porous Resin mold. In case of a common battery type HPC one person removes up to 12 molds all at once.
- Further treatment: The removed clay body may require additional processing steps to achieve the desired shape, surface finish, and mechanical properties, e.g.holes are being made, surplus material needs to be removed and surfaces are smoothed with a wet sponge.
- Pre-drying: The clay bodies will then dry until only a certain amount of water is left within.
- Burning: After pre-drying, the products are again checked for defects, glazed and burnt in the oven.
- Cleaning: The HPC mold cleans with water and air. Afterwards the mold closes again for the next casting process.
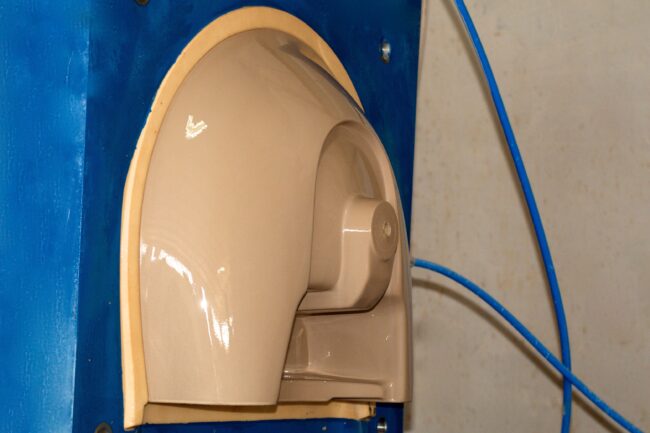
Overall High Pressure Slip Casting
On the whole high pressure casting with porous resin molds is a reliable and cost as well as time efficient method for producing high-quality ceramics. Due to the use of high-pressure and the level of automation, labor costs are reduced and production efficiency is increased.
High pressure slip casting is a manufacturing process used to produce ceramic parts with high density, strength, and dimensional accuracy. It involves injecting a ceramic slurry or “slip” into a mold at high pressure (typically ranging from 500 to 1500 psi) to fill the mold cavity and create a dense, uniform ceramic part.
The high pressure helps to overcome the resistance of the slip to flow into complex mold shapes and narrow features. As the slip fills the mold, excess water is forced out through small pores in the mold surface, leaving behind a solid ceramic part with minimal shrinkage.
The process is particularly suited for producing small to medium-sized parts with intricate shapes and fine details, such as ceramic dental prosthetics, electronic components, and precision mechanical parts. High pressure slip casting can also be used to produce larger parts, but this requires specialized equipment and may be more difficult to achieve uniform density and quality.
https://www.castimo.de/high-pressure-casting-101-the-casting-process-for-sanitary-ware/
https://www.instagram.com/castimogmbh/
https://www.linkedin.com/company/castimogmbh/